製造業・熟練技能者の暗黙知をAIに代替させる実証実験
確かな成果を基に新サービスのβ版テスト販売を開始
2022.12.12
- AI
- 製造業
- 業務効率化
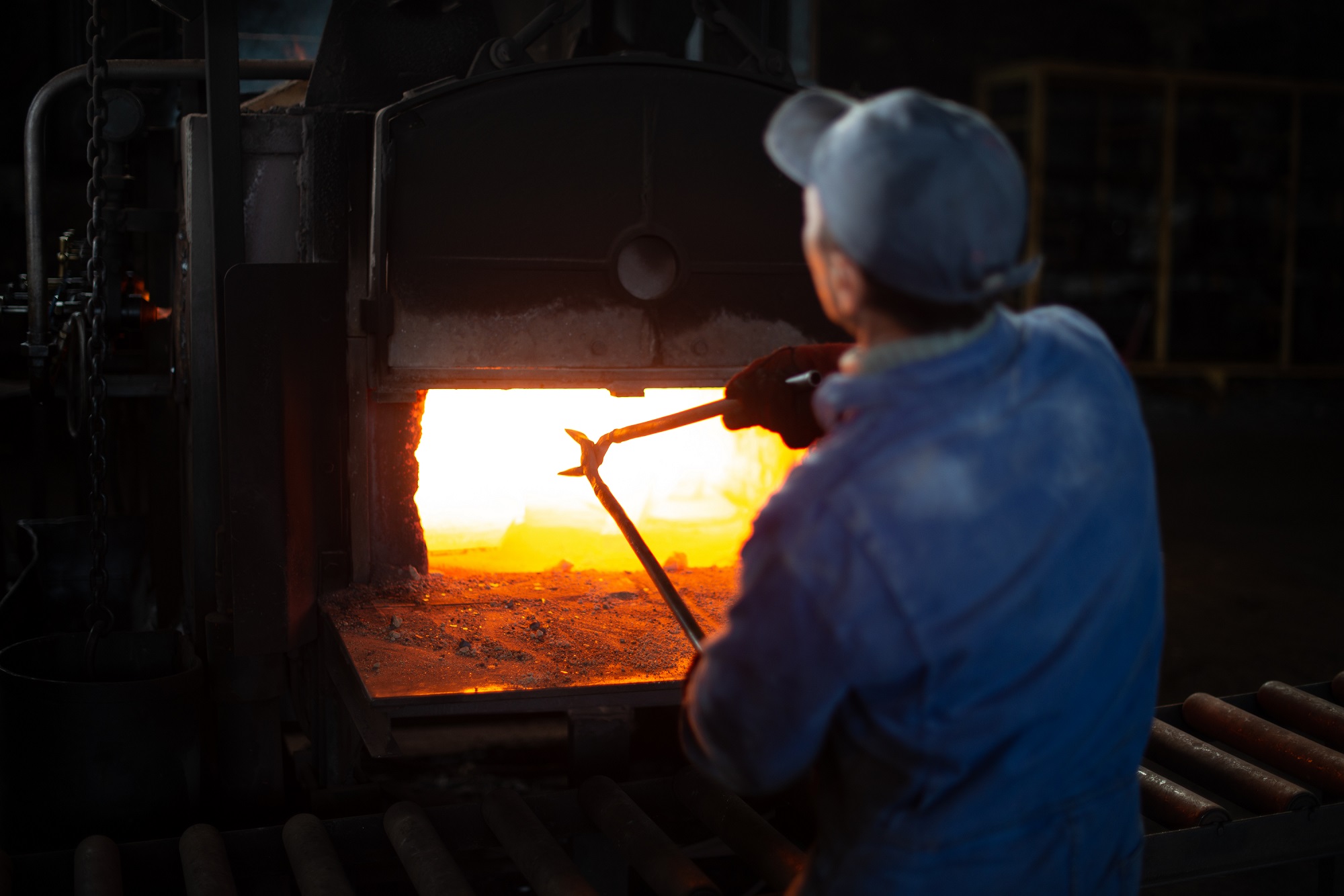
当社は、株式会社上島熱処理工業所様(以下、上島熱処理様)と共同で、金属熱処理工程における熟練技能者の暗黙知をAIに代替させる実証実験を実施。そこで得られた確かな成果を基に、新サービス「製造条件最適化ソフトウェア利用サービス」のベータ版のテスト販売を開始しました。本稿では本実証実験の目的と工程そして得られた成果について、詳細をご紹介します。
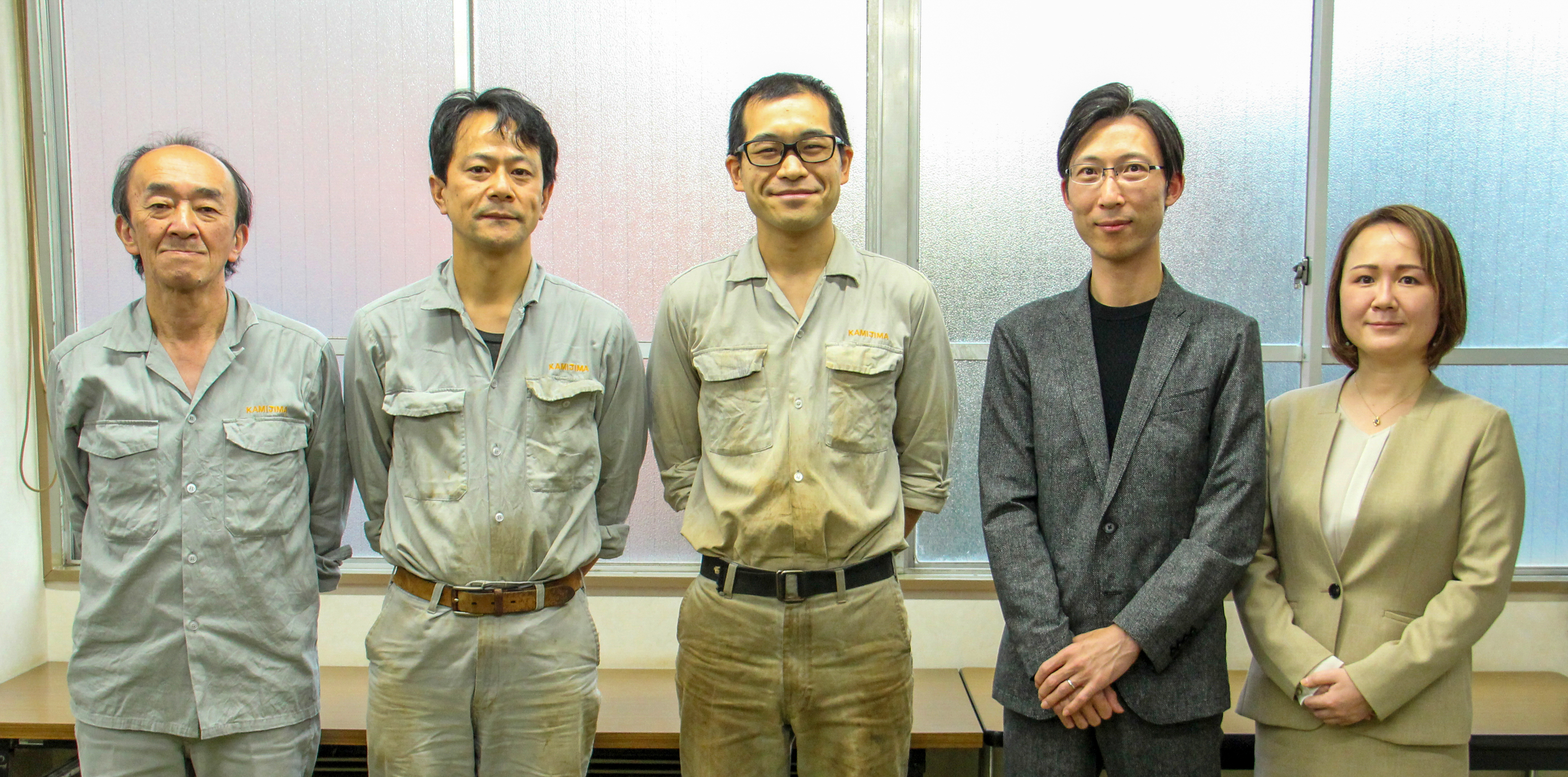
<実証実験概要>
- 協力 株式会社上島熱処理工業所 様
- 期間 2021年12月~2022年9月
- 対象業務 鉄鋼の焼入焼戻し加工における、加熱温度および保持時間の判断
- 検証観点 ・AIによる予測値の妥当性
・現在の業務への適合性
・システムの使いやすさ
本実証実験実施の狙い、背景
すべての製造企業に「データ分析のチカラ」を—
AI技術を現場技術者でもシンプルに利用できるサービスを開発
DCSは、製造現場における人材不足、生産性向上、熟練技能者による技能の属人化、社会のデジタル化と働き方改革への対応、若手への技術・技能継承による事業継続性の確保といった課題への解決策として、AI技術を活用して製造品質の安定化を支援するサービスの開発に注力しています。
「中でも大企業に比べ資金力や人員数が劣る中小企業では、データ利活用のための投資予算や対応するデジタル人材の確保が難しく、導入検討が進んでいない現状があります。当社ではそうした現状を踏まえ、『難しい操作を難しく感じさせない、AI技術のインスタント化』をコンセプトに、AIのオートチューニングアルゴリズムとUXデザインを駆使*し、『データサイエンスの知識がない現場技術者でも高いハードルを感じずに利用可能なデータ分析ツール』としてのサービスを開発しています。これまでの活動の中で、幅広い製造業でばらつきを抑える微調整を行っていることはわかっていましたが、今回はそれが本当に我々の身近でも存在するのかを確かめるべく、上島熱処理様の協力を仰ぎ、実証実験を行いました。」
(DCS 永田 貴弘)
*特許出願中
解決すべき課題と本実証実験のきっかけ
企業競争力の源泉である独自技能=熟練者のみが把握する「暗黙知」のAIによる代替にチャレンジ
▶上島熱処理様Webサイト:http://www.kamijima.co.jp/
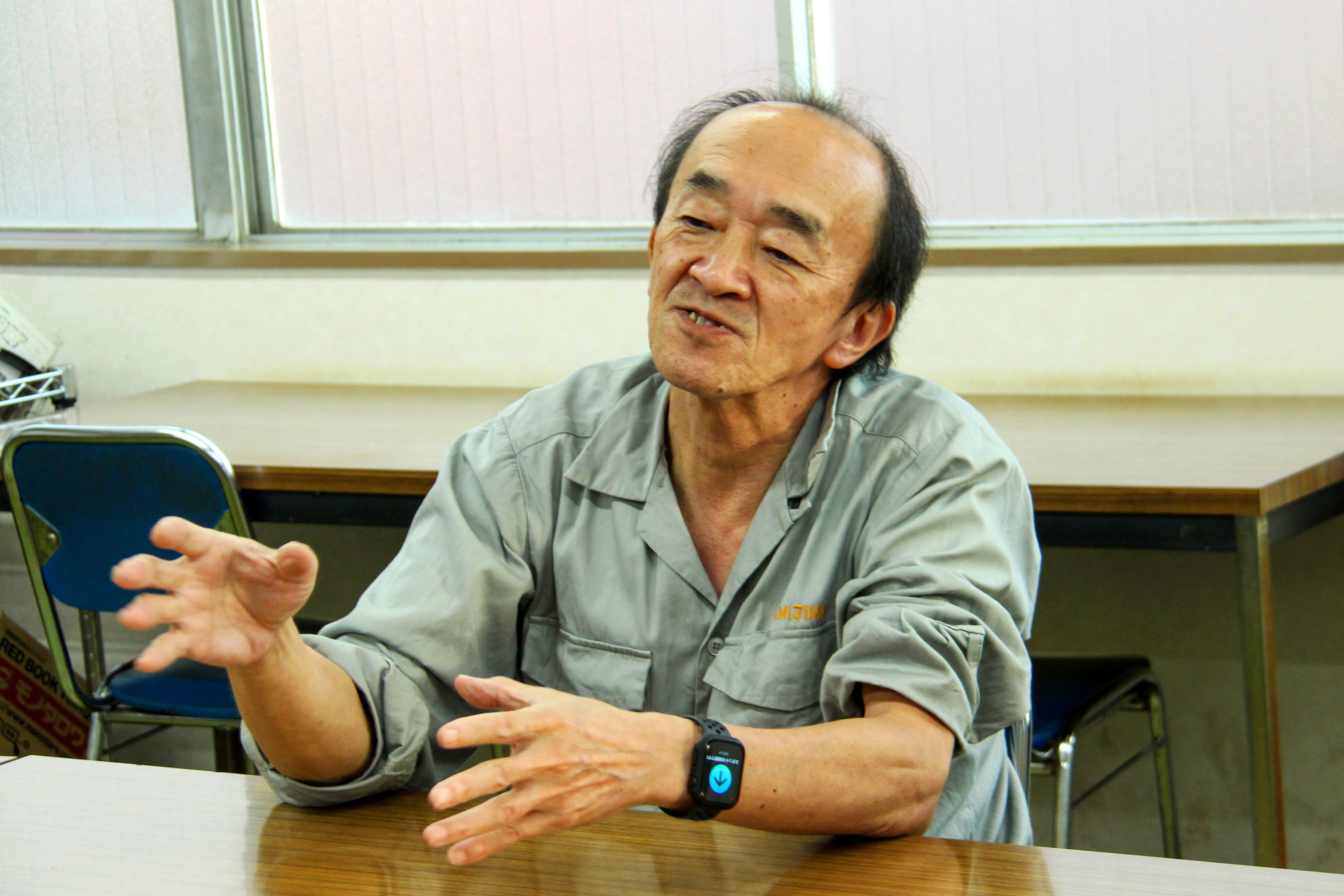
株式会社上島熱処理工業所 技術部 部長の坂田玲璽氏は、同社が展開する事業における課題を、次のように話します。
「当社は総勢約50名の少数精鋭ですが、おかげさまで『難しい熱処理はカミジマに頼め』とのクチコミが広がり、全国から自動車部品や医療機器、航空機に至るまで、多種多様な金属熱処理の注文をいただいています。創業以来『お客様の製造ラインの一部門たれ』をモットーに、お預かりした製品をわが社の製品と考えて、鋼に魂を入れる作業を続けています。お客様の多くは、硬さや耐久性を求めて当社に熱処理を依頼されるのですが、その精度が極めて厳密で、かつ対象がお客様からお預かりした製品であるため失敗が許されない難しさがあります。高い品質が求められるそれらの工程ではどうしても標準化が難しく、熟練技能者の経験や勘といった暗黙知が多いため若手への継承や人材の育成に長い時間がかかる課題がありました。」
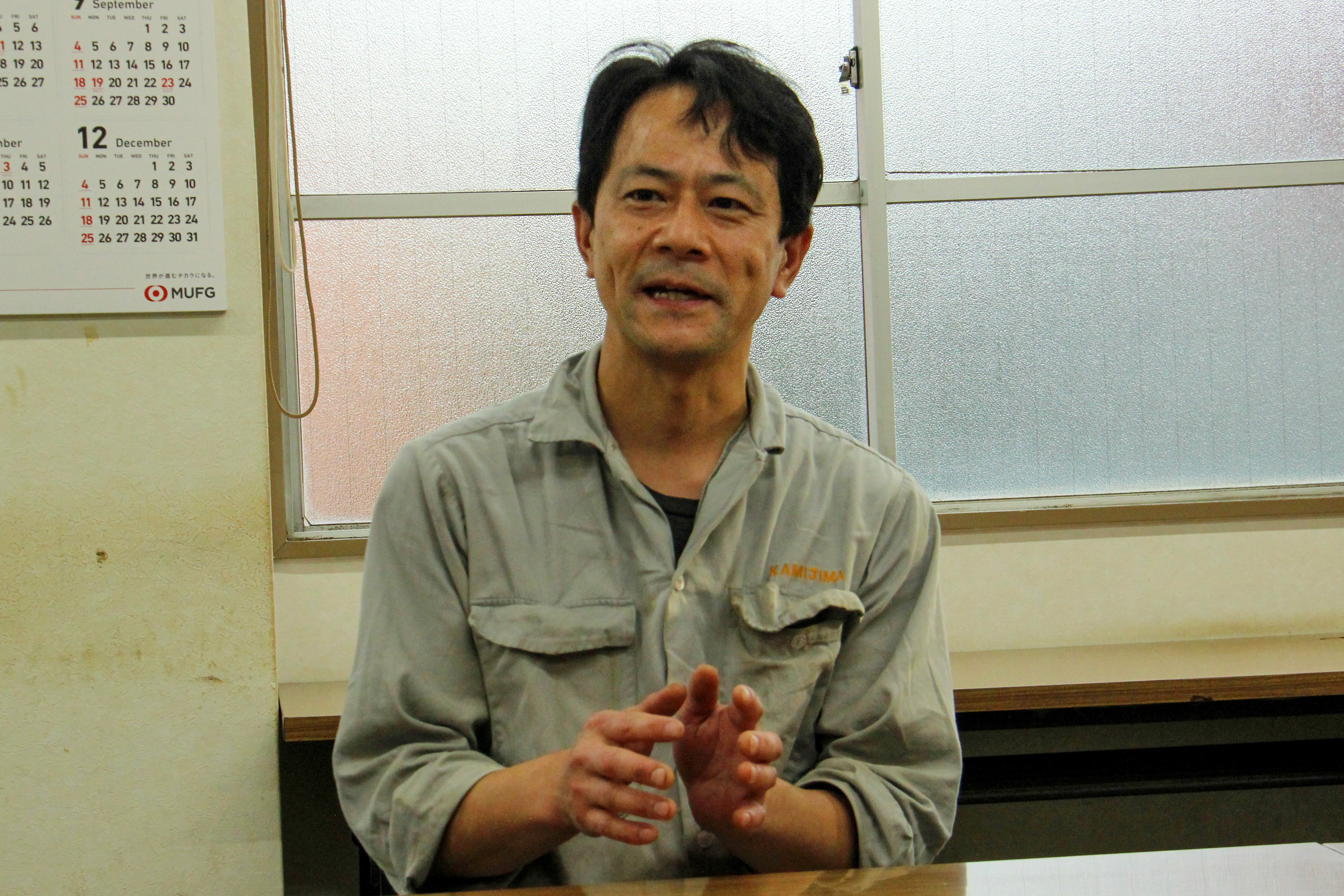
具体的な工程と、その難しさを上島熱処理の澁澤直哉氏はこう説明します。
「お客様から製品を受け入れする際に、求められる硬さの指定に応じて、材質や大きさ、形状などの特性を踏まえて熱処理工程を設計。『加工検査記録票』と呼ぶ指示書を作成し、現場に流します。現場ではその指示書を基に、1回の焼入と3回の焼戻しと呼ばれる作業を行います。中でも焼戻し3回目の温度と時間設定が肝となります。2回目の焼戻し工程での硬さの測定結果を踏まえた上で、お預かりした製品を破損させず、指定された硬さの精度を保つために、熟練技能者の判断が必要となる部分です。」
坂田氏は、こうした工程にAI、機械学習が活かせるのではと考え、検討していたと話します。
「個人的にAI、機械学習で何らかの解決策が見出せるのではと興味を持ち、調べていました。熟練技能者の判断に依存するとは言っても漠然としている訳ではなく、一定の考え方のプロセスがあり、データに基づいて判断している訳です。であれば、一定のデータがあればAIによる自動化は可能だと考えていました。ちょうどそのタイミングで、当社が出展する展示会場で、DCSから本実証実験のオファーをいただいたのです。」
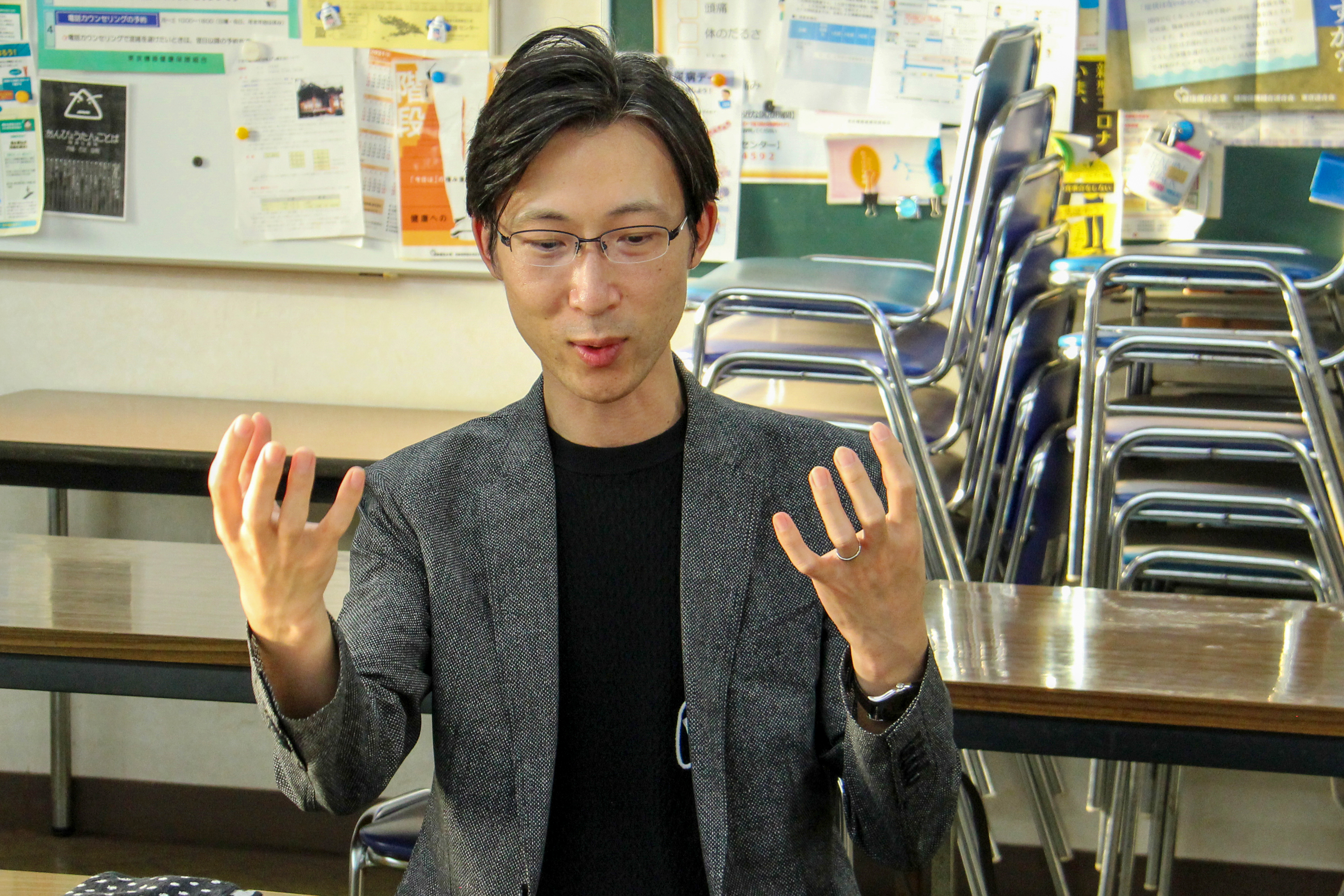
シニアデータ分析エンジニア 永田貴弘
永田は、同社にオファーした理由をこう話します。
「これまでの取り組みの中で、多くの製造業の企業では材質や環境にバラツキがある中で結果を同一に保つために熟練技能者の暗黙知が活かされており、それこそが事業の競争力の源泉であることを学んでいました。それ故に、上島熱処理様でも同様のポイントがあり、当社の技術が課題解決に活かせるのでは?と考え、お声がけしました。」
対象業務の選定
実業務を把握、協議を重ねて対象業務を選定
同社の長年に渡る実績データの蓄積が活かされる
その後、両社の思惑が合致し、2021年8月より、AI代替の実証を行う対象業務の選定協議を重ねました。
AIの機械学習を行うためには相当量のデータが必要ですが、同社には豊富な実績データが存在していたことも、好条件でした。「当社では13年ほど前に生産管理システムを導入し、データベースに実績データを蓄積しています。その理由は、過去の実績数値に基づいてリピート対応する、類似品を参考に新規製品の焼入工程の設計をするため。それに加えて、トレーサビリティの観点から納入済み製品のトラブル発生時に、遡って調査・報告する必要があるためです。そのデータは自動車で十年間、航空機だと永久に保持する必要があります。」(坂田氏)
対象業務の選定に際し、DCSはヒアリングを重ね、製造現場も見学して実業務を学びました。その上で、候補に挙がったのは2つの業務でした。
1つ目は、製品受け入れの際、過去の実績数値を基に現場への作業指示書を作成する業務。しかし、この業務については同社が所有するデータのバリエーションが不足するため、今回は見送られました。永田はその理由をこう説明します。
「本業務は、焼戻し2回目後に狙った硬さを得るための製造条件を予測する業務です。これをAIで代替するためには、どの温度でどれくらいの時間加熱したら硬さがどう変化するのかという金属物性の科学的な性質を学習する必要があります。お客様から求められた硬度を狙って加熱した実績データに限らず、様々な温度、時間で加熱したデータが必要ですが、お客様の製品を扱う生産の中ではそのような実験的なデータは揃えることができません。そのような事情から今回は見送りとしました。」
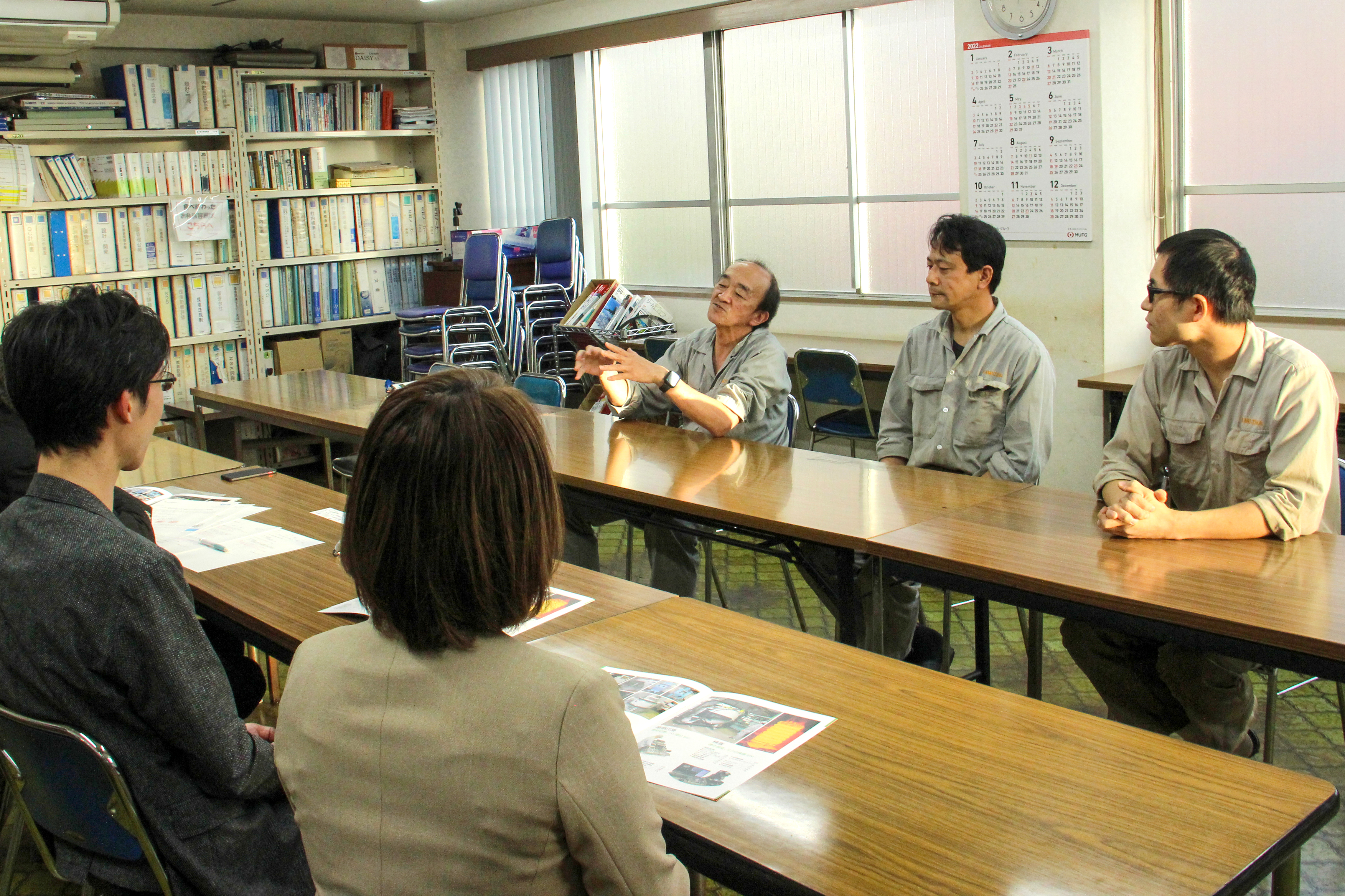
2つ目は、狙った硬さを得るための肝となる最終工程である3回目の焼戻し作業の温度とその保持時間を判断する業務。これをAIで再現するためには、途中結果がどのような状態であったらどれくらい温度を微調整するのかという熟練技能者の暗黙知(経験と勘)を学習する必要があります。この場合、1つ目の時と違い科学的性質自体の学習までは必要ないため、これまで製造してきた実績の範囲内のよくあるパターンのデータが揃っていればAIの学習には十分となります。そこで、今回はこれについてAI代替の実証実験を行い、高精度の予測が実現しました。
実行プロセスと成果
過去データを用いた机上検証を経て実務適用
熟練技能者の暗黙知をAIが97%の正解率で再現
実証実験は、2021年12月からスタート。3回目の焼戻し作業は、1回目、2回目の結果を踏まえて、「熟練技能者の暗黙知」により温度や時間の設定が行われます。本実証実験は、それをどこまでAIが再現できるか、機械学習の精度を検証するものです。
永田は実施プロセスを次のように説明します。「もっとも受注の多い鋼種の、1年間の実績データをご提供いただきAIが学習。第一段階では机上での検証とし、実績データのうちAI学習に用いるデータとは別に取り分けておいた1カ月分の実績データを用いて熟練技能者の判断が再現できるか確認しました。AIの予測結果と実績データと照合したところ、93%という高い正解率が確認できました。そこで第二段階として、さらに3種の鋼種を加え計4種で、実際に現場でのご担当者の判断とAI判断の差異を検証する実務適用を、2022年6月末より実施しました。その結果、97%という非常に高い正解率を得ることができました。」
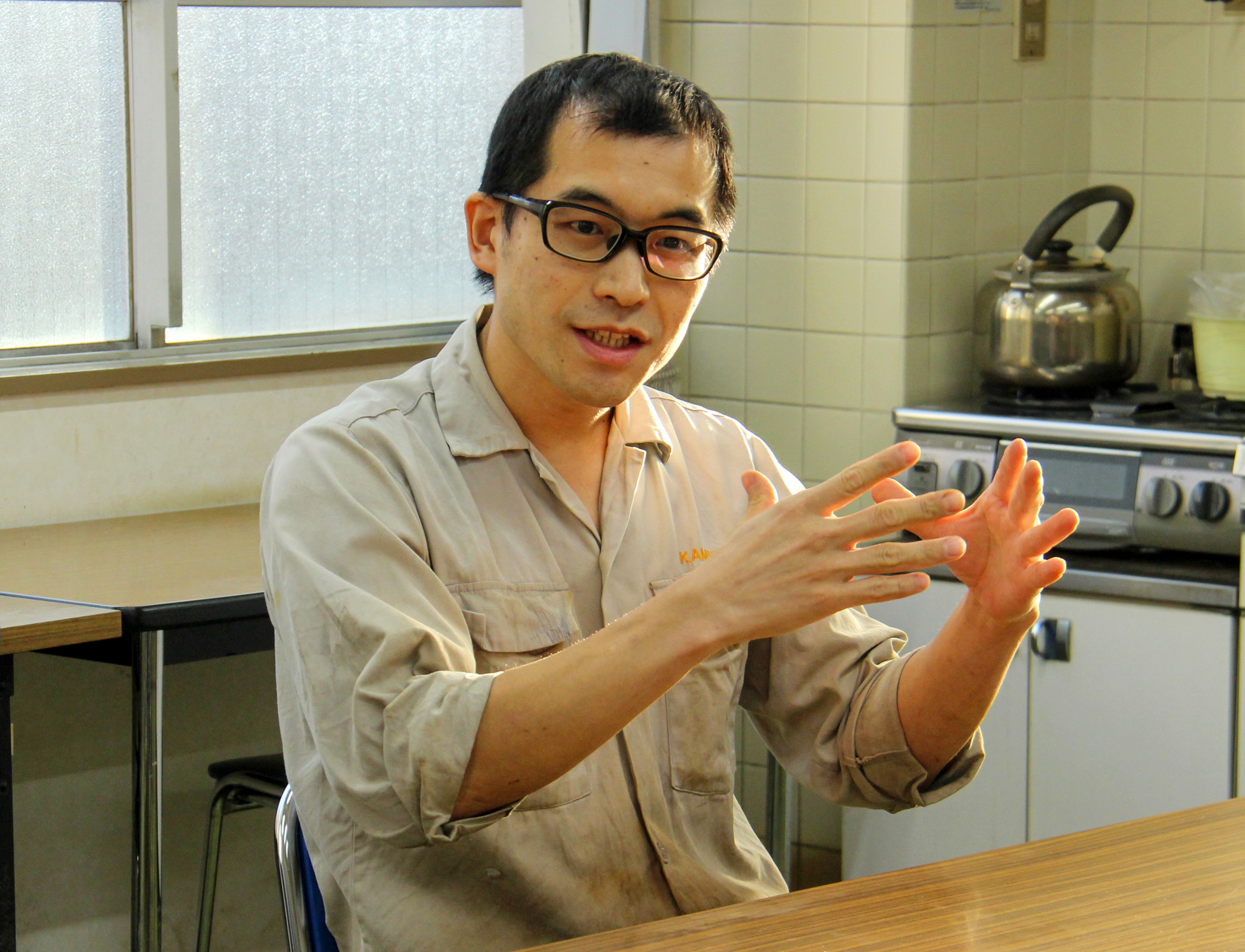
実際に現場で焼戻し作業を担当する上島熱処理の吉田宏二氏は、
「1つ1つの予測数値を細かく照合すると誤差がほとんどなく、正解率が高くて驚きました。実際の現場では工程や作業効率との兼ね合いで設定数値に幅を持たせることがありますが、充分に実務に利用できる結果と言ってよいと思います。」とその評価を語ります。
この間、DCSは上島熱処理様にタブレット端末を貸し出し、日々の業務においてデータを蓄積いただくと共に、ソフトウェアの操作のしやすさ、わかりづらい点などのフィードバックを受け、製造現場の担当者でも簡便に扱える操作性を目指し、さらなるUI/UXの改良も行っています。
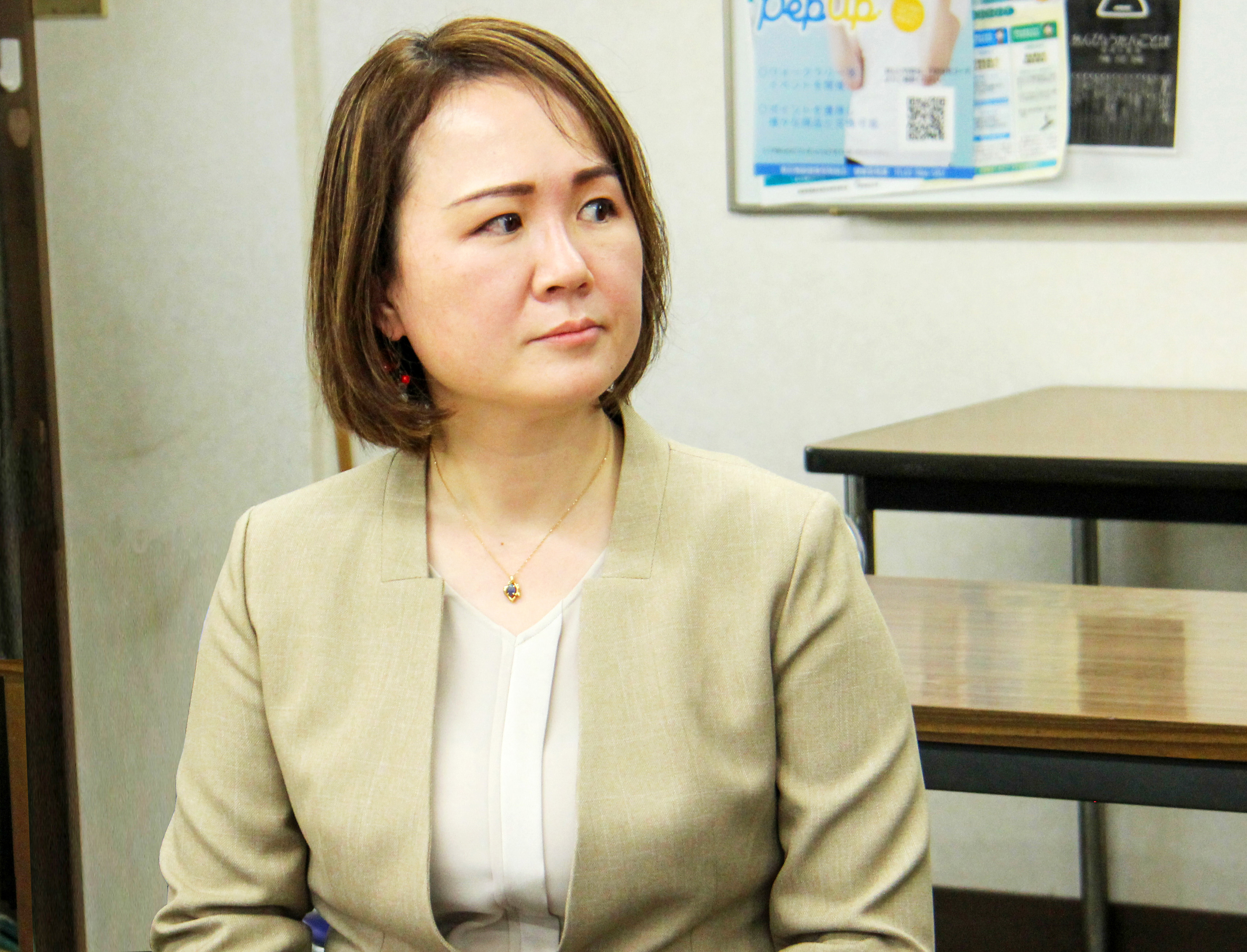
HCD-Net認定 人間中心設計専門家 武内亜美
吉田氏は「これまで現場では端末操作や数値入力などは行っていませんでしたので、作業工数としてはプラスではありますが、操作については特に使いにくい、わかりにくいということはありませんでした。」と語り、
これを受けてUI/UX開発担当のDCS武内は
「今回の実証ではプロトタイプとしてスタンドアロンシステムで開発したため、社内の別システムでお持ちの数値データも入力していただかねばならず、入力項目自体が多かったのです。今後はシステム連携などで入力工数をいかに削減するかが、改良ポイントと認識しています。それ以外にも貴重な声をいただいていますので、さらに使い心地をブラッシュアップしたいと考えています。」と述べました。
2021年 |
7月20日 | 初回ヒアリング・情報交換 |
8月5日 | DCSの意図説明、製品デモ、質疑応答 | |
10月14日 | 業務概要紹介および現場視察 | |
11月11日 | 生産管理システム紹介、データ受領 | |
11月29日 | 業務フローおよびデータ確認 | |
12月22日 | 実証実験テーマ決定/実証実験第1段階(数値予測)開始 | |
2022年 |
2月15日 | 実証実験第1段階の結果報告 |
6月6日 | 実証実験第2段階(実務適用)キックオフ | |
6月28日 | 実証実験第2段階ステップ1実施 | |
8月22日 | 実証実験第2段階ステップ1経過報告会 | |
9月8日 | 実証実験第2段階ステップ2実施 | |
9月15日 | 実証実験第2段階成果報告、ヒアリング |
今後の展開
確かな成果を踏まえ、今後のAI活用範囲拡大にも手応え
製造現場でのデータ利活用のために今、行うべきこととは?
今回の成果を受けて、坂田氏は「当社では意識して早くからデータを蓄積して来ましたが、今回の取り組みでAI機械学習の変数パラメータなどの仕組みや考え方に触れることができ、今後のデータの取り方も変わってくるでしょう。」と、その手ごたえを語ります。
今後の展開について、永田は「今回はプロトタイプのスタンドアロン型システムで検証いただきましたが、実務でも十分、活用いただけるレベルにあることがわかりました。今後は基幹システムなどと連携し、製品の受け入れや工程設計時に入力済みのデータをそのまま利用いただけるなど、さらなる利便性を向上していきたいと考えています。」と話します。
これを受けて吉田氏は「将来的に当社の生産管理システムとの連携が実現すれば、各数値の入力工数が削減できるだけでなく、現状、人手で行っている納期と現場工程の順番調整なども容易になり、さらなる負荷軽減につながると期待しています。」澁澤氏は「当社はデータの蓄積はあるものの、活用という面ではまだこれからの段階です。これからますます市場変化が激しくなる中で、AIを現場の改善だけにとどまらず、お客様の傾向分析や受注予測などにも活用していければと考えています。」と、それぞれの視点で可能性への期待を述べました。
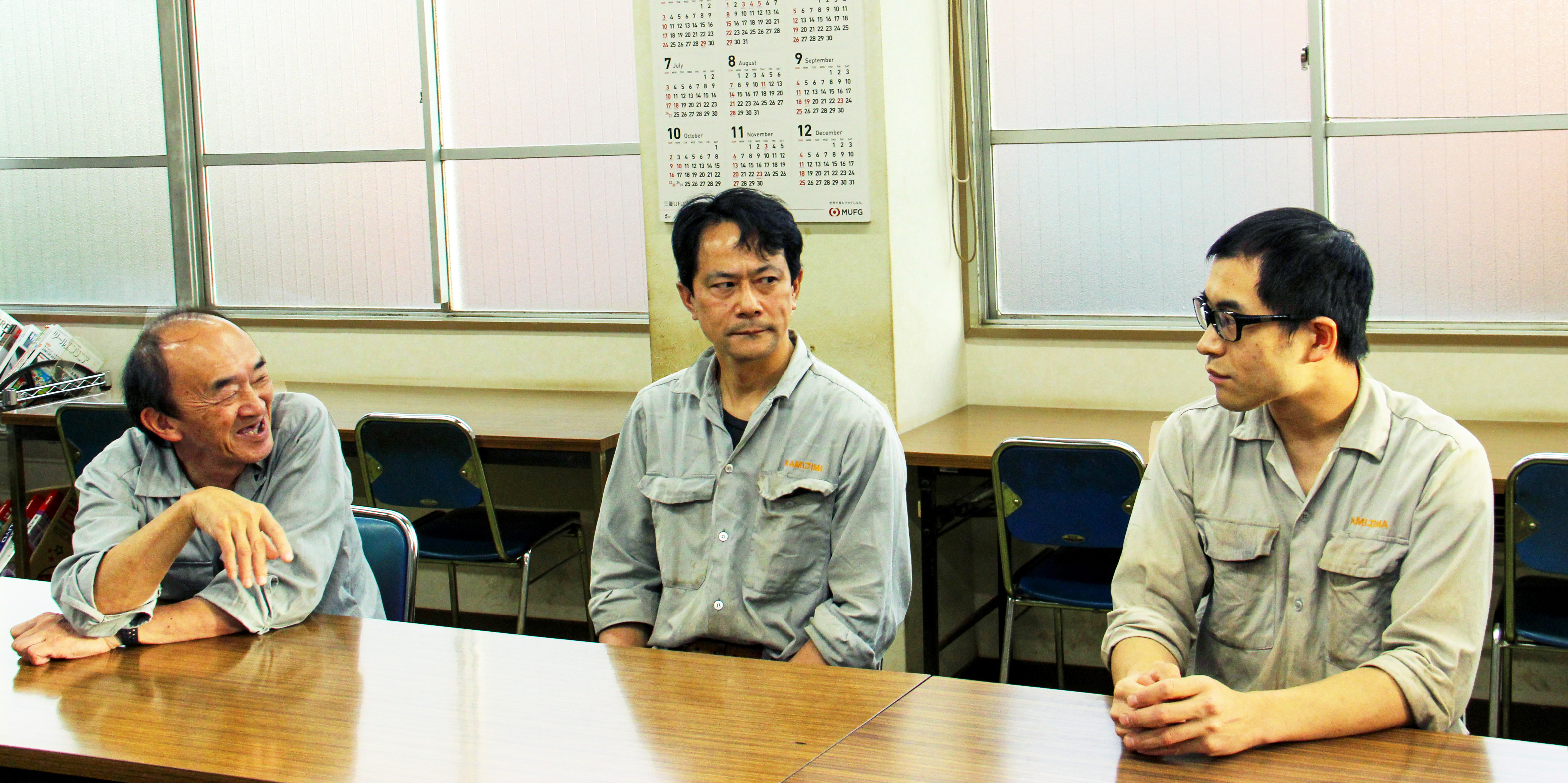
坂田氏は、これからのAI利活用に向けて大切なこととして「今は必要ないと思っても、取れるデータは取得しておくこと」と語ります。「最近は現場の機器であっても、工数やコストをかけずにSDカードなどにデータとして保存できるようになっています。また、IPアドレスを持たせられる機器も多いですから、ネットワークにつなげられる機器はとにかくつなぎ、取得できるデータは今のうちから何でも蓄積しておくことが重要です。もちろん並行して、社内のネットワーク化やファイル共有といった、誰もがデータを利活用しやすい環境を整備することも大切です。なかなか経営層の理解が得られず、予算確保に苦労している企業もおられるでしょうが、今回のように現場主導、スモールスタートで実証し、具体的な成果を見せれば反応も変わると思います。」
これを受けて、永田は次のように結びました。
「過去の実証実験と今回の上島工業所様との実証実験を通じて、2つの確信を得ました。ひとつは、私たちが注目している「材料や環境のばらつきが結果に影響しないように打ち消す微調整」は対象や手法は異なれど、様々な生産現場で行われており、その習得に時間がかかるという共通の問題意識を抱えていること。もうひとつは、感度の高い企業は一定程度のデータがあれば直感や勘といった暗黙知でもAIで再現できると考えて、既にデータを取り始めているということ。坂田さんから紹介いただいた製造業の経営者の方には、IoTでデータを記録する技術を共有、教育する協会を立ち上げた方もいるほどです。
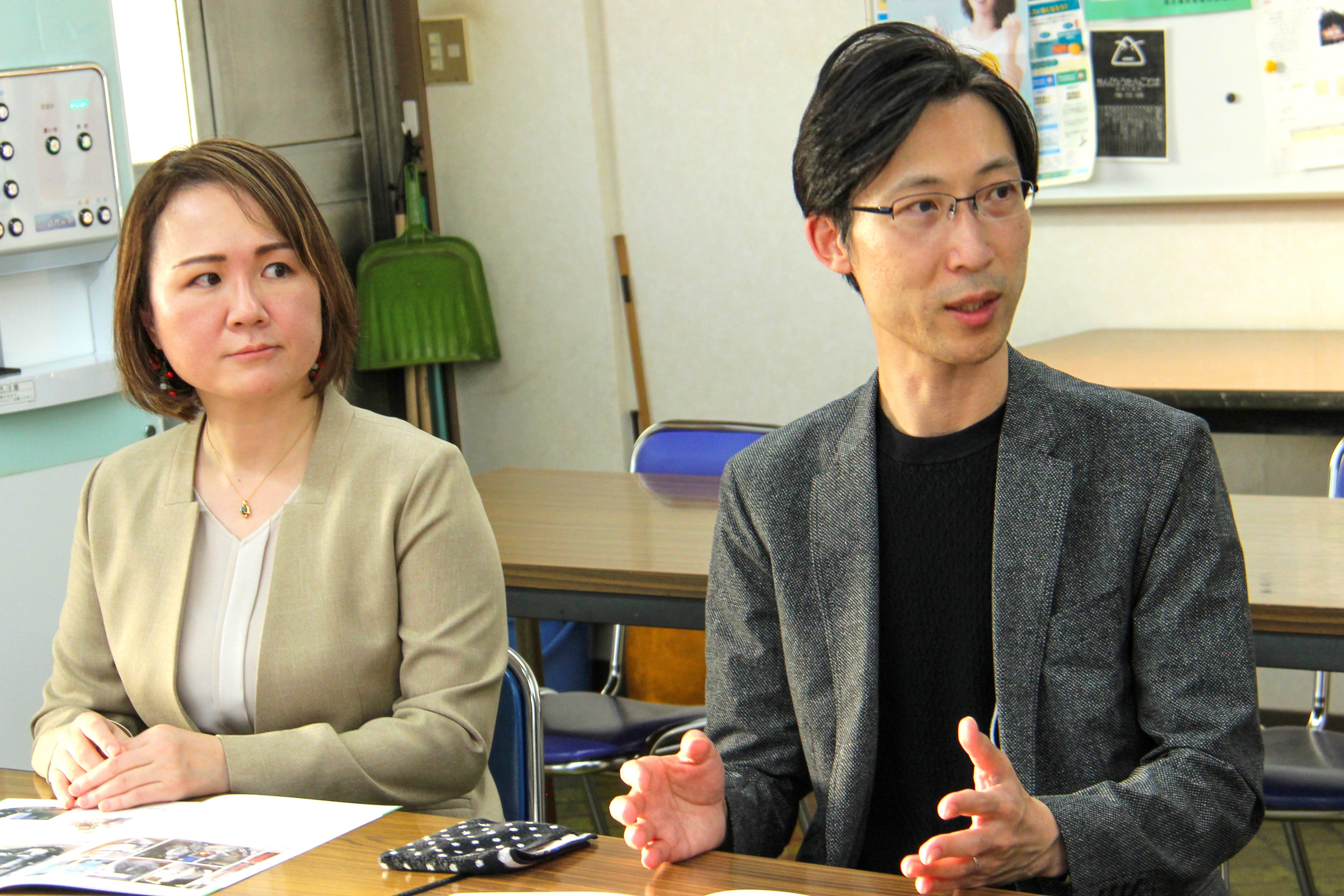
この確信から、我々の製品は多くの製造現場のお役に立てる、データを軸に製造する新たなスタイルへのシフトを支援することができると判断し、この度ベータ版の先行テスト販売に踏み切ることとなりました。
テスト販売は実際に価値を提供していきながら、製品機能以外の部分を洗練させて本番リリースに備えることが目的です。製品だけでなく業務オペレーションも洗練させることで数多くのお客様に安定して価値をお届けできる体制を整えていきます。
私たちは、このデータ活用の流れはどんどん広がり、データ分析に基づいて製造することが中小製造業であってもあたり前になる時代が来ると信じています。そしてその時が近いことを見据えて、使いやすいソフトウェアの提供だけでなく、AIを使って製造する新しい業務の仕方にスムーズに移行できるよう支援することも目指しています。
まだデータ化が進んでいない企業様も、ぜひ今測定できるものから記録を始めていただき、我々と共に、新しいスタイルへの第一歩を踏み出していただきたいと思います。」
-
お問い合わせ
-
本サービスの詳細につきましては、以下お問い合わせフォームよりご相談ください
関連するソリューション・サービス
関連する技術レポート・導入事例
メディア掲載・登壇実績
- 上記から各外部サイトへ遷移します。