【結果レポート】製造業・熟練技能者の暗黙知をAIで代替する実証実験
2022.03.14
- AI
- 製造業
- 業務効率化
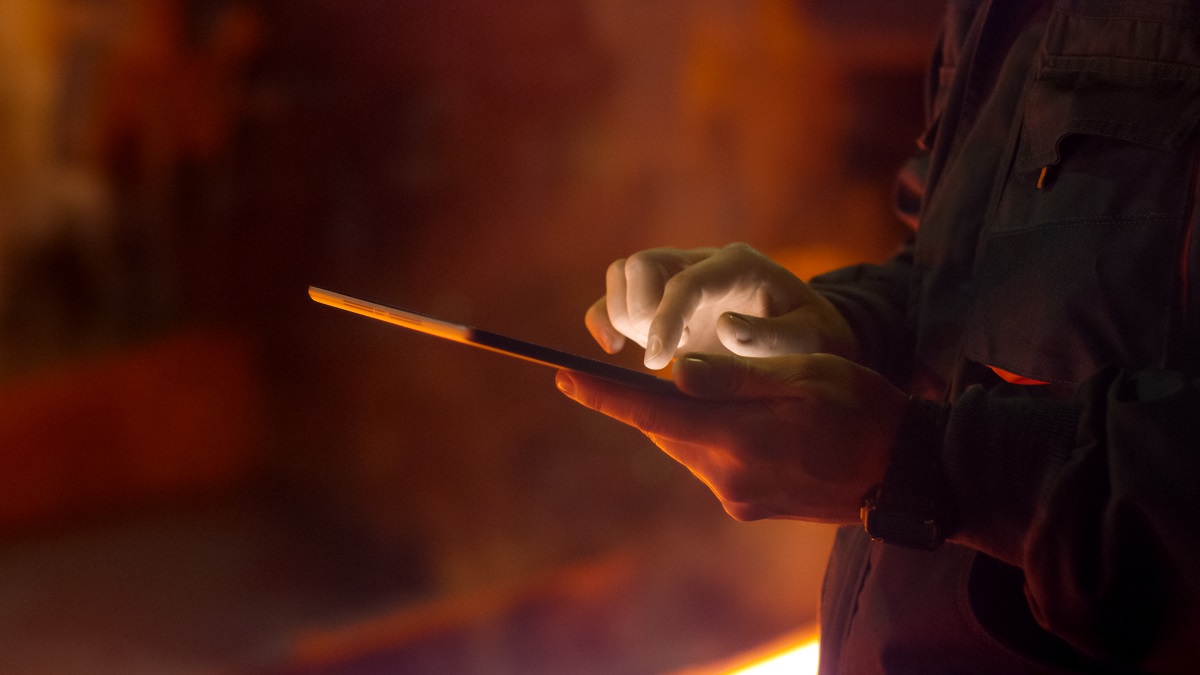
前回の取り組みレポートにて、当社と中島合金株式会社様(以下、中島合金様)が共同で実施した熟練技能者の暗黙知をAIに代替させる実証実験について概要をお伝えしました。本稿では、そこで得られたAI予測値の妥当性および業務への適合性、システムの使いやすさの結果について、詳細を解説します。
<実証実験概要>
- 期間 2021年4月・12月(計2回)
- 対象業務 純銅鋳造製造における添加剤の投入量判断
- 検証観点 ・AI予測値の妥当性
・現在の業務への適合性
・システムの使いやすさ
本実証実験の目的
日本の製造業は、労働人口の減少に伴う人手不足、熟練工の高齢化と若手への技術継承という課題に直面しています。中でも経験と勘によるデータ化が難しい技能については属人化が避けられず、働き方改革や事業継続性の観点においてもリスクを抱えています。
中島合金様が手掛ける純銅鋳物にはCAC100番台のJIS規格が定められており、品質を一定水準に揃えることが求められます。そのためには、品質に影響する主要な制御因子を把握し、その最適条件を定め、できる限りその条件値に近くなるようにしなければなりません。しかし実際には、技術的、コスト的制約から製造者が自由に制御できない因子も存在します。これらの因子は測定してみて初めて状態がわかるため、当然ばらつきを抑えることができません。
中島合金様は、製造工程の途中段階でこの抑え込めないばらつき具合を測定し、その値に応じて調整用の添加剤を適切量投入することで製品の最終品質を均一化する、熟練の技能を持っています。しかし、この技能を若手が継承するには長い時間がかかるという課題がありました。
この課題解決を目指し、当社が持つAI技術を活用したシステムの検証を行うのが、本実証実験の目的です。
中島合金株式会社 代表取締役社長の中島一郎氏は、本実証実験の意義を次のように話します。
「当社の純銅鋳物製造工程では、細かなデータを蓄積して品質管理を実施しておりますが、最終的な添加剤投入量の判断は熟練作業者の長年の経験と感覚に拠るところが大きく、若手への継承が難しいことが積年の課題でした。業務が属人的ですと担当者が休みをとりづらいだけでなく、万一、休職や離職ということになれば事業継続にも深刻な影響が及びます。こうした課題に対して、DCSからAI技術を用いた検証の提案を受け、当社としても課題解決につながるのでは、との期待がありました。」
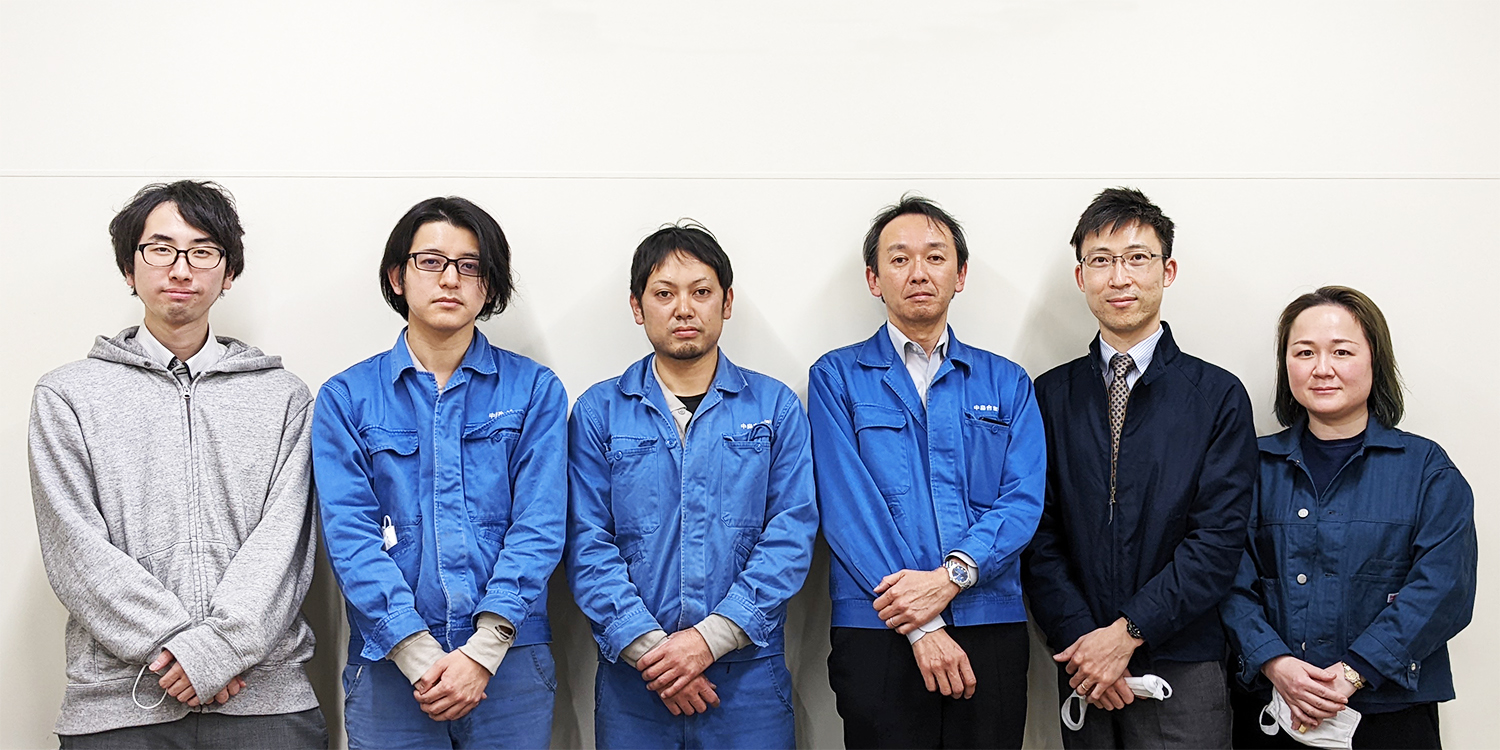
実験概要
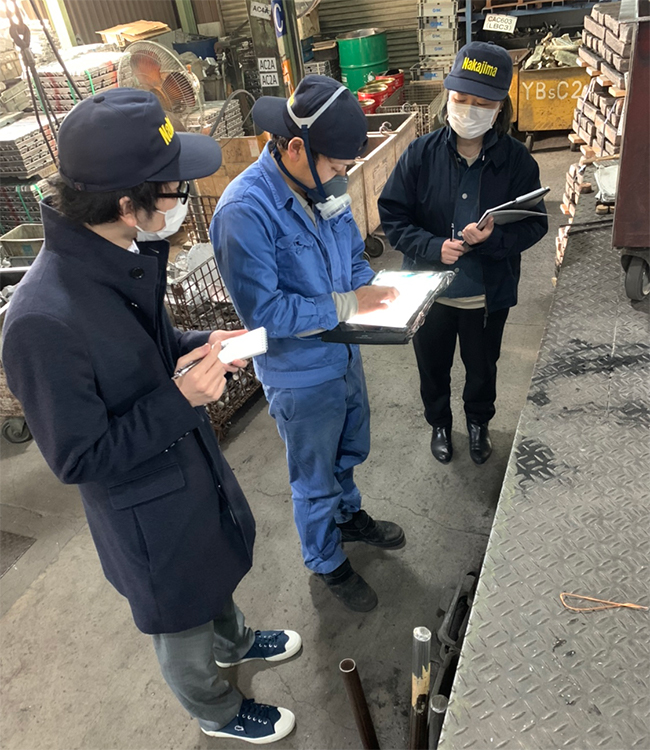
実証実験は、2021年4月と12月の2回に分けて実施されました。
4月の段階では以下3点を前提にAI予測値の妥当性について実験を行いました。
1.実際の純銅鋳造を10回行い、添加剤の投入量に関して、AIでの予測と熟練者の判断を比較する
2.熟練者が問題ないと判断した場合、AIの予測値の通りに投入する
3.AIの予測処理については当社が支援し、熟練者は操作を行わない
この結果得られたAI予測値およびシステムの操作性に関する課題を改善した上で、同年12月に2回目の実験を行いました。
その際、以下3点を前提として、AI予測値の妥当性および業務への適合性、システムの使いやすさを確認しました。
1.実際に純銅鋳造を4回行い、添加剤の投入量に関して、AIでの予測と熟練者の判断を比較する
2.熟練者が問題ないと判断した場合、AIの予測値の通りに投入する
3.AIの予測処理については、タブレット端末を用いて熟練者自身に操作してもらう
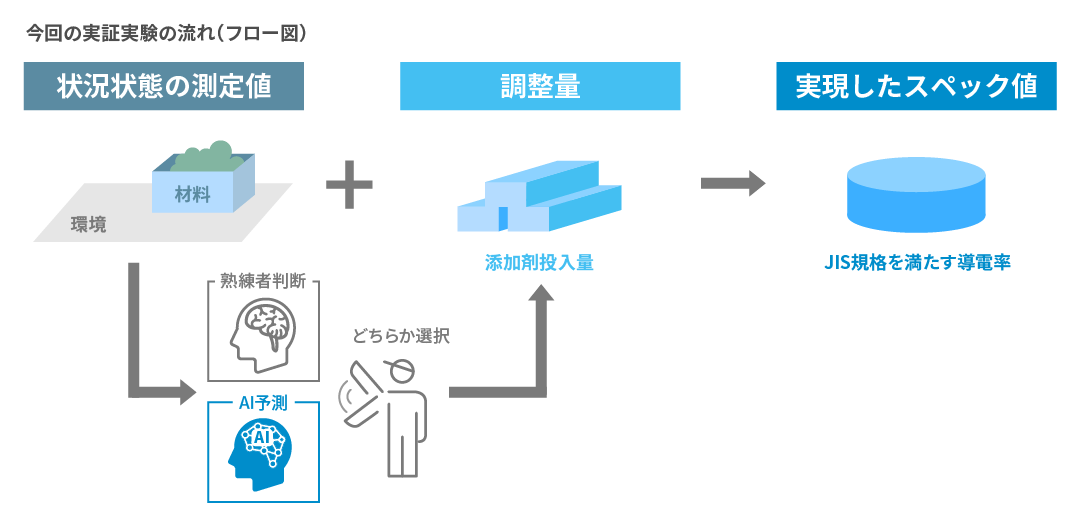
実験結果
実験結果①:AI予測値の妥当性
計14回の製造中、13回でAI予測値が採用され、そのいずれでもJIS規格をクリアしました。
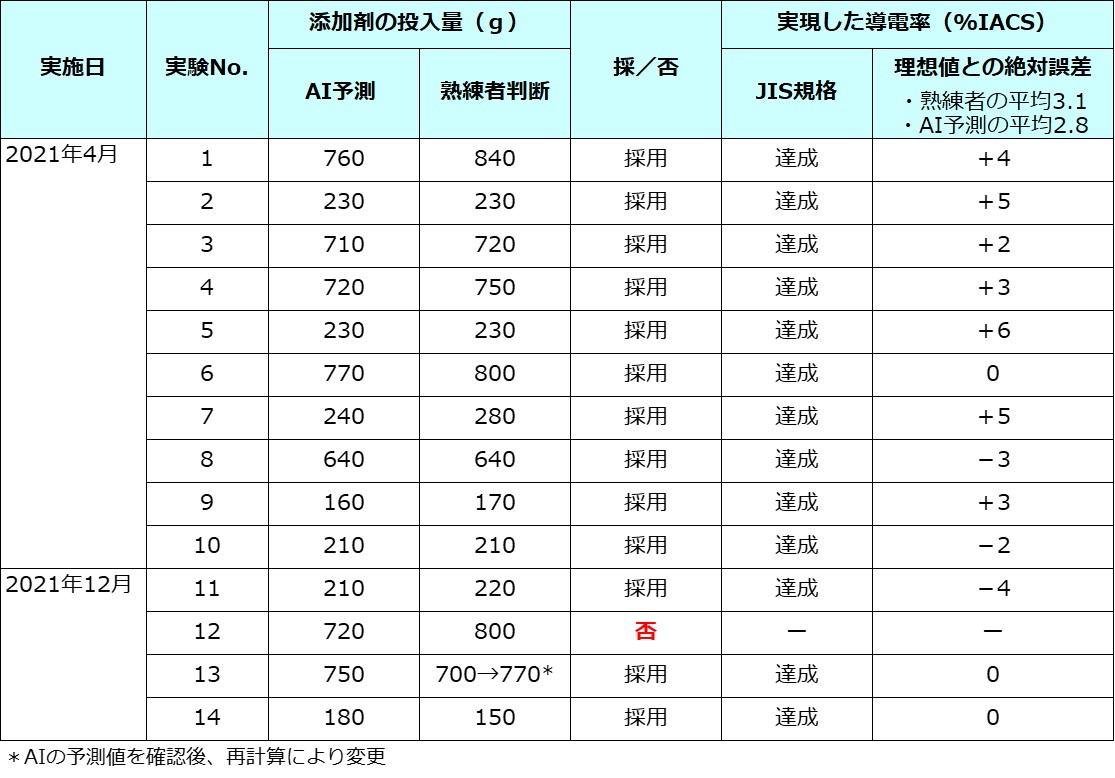
13回目の実験では、AIの予測値を見た熟練者が再計算した結果、AI予測値の方がより望ましいと判断され、採用となりました。また、14回目の実験ではAI予測値が採用された結果、最終的な導電率が理想的な値となり、AIの精度に高い評価をいただくことができました。
熟練者である中島合金株式会社 製造部 鋳造課 主任の生井光章氏は、この結果を次のように評価します。
「4月の1回目時点でもJIS規格はクリアしていましたが、2回目の方がよりAI予測値の精度が高まり、当社が目指す品質基準から見ても、十分実用に耐えうる結果となりました。AI予測値は自分の判断とそん色なく、もっとも調子のよい時と近い結果が出たのには驚きました。」
実験結果②:業務への適合度、システムの使いやすさ
本実証実験のもう一つのポイントが、業務への適合度およびシステムの使いやすさです。これは当社が目指す「これまで難度の高かったAIによる分析を現場作業者にも容易に扱える操作性を実現し、実業務への適合性、導入コストも含めたインスタント化を実現する」というコンセプトからも重要な検証です。
具体的には、予測処理の操作性と予測処理時間の2点が主な検証ポイントです。その点について中島合金の生井氏は、次のように評価します。「鋳造業務の現場では、一度溶解してしまうと状態が刻々と変化し、時間との勝負となります。また、同時並行的にさまざまな作業も行う必要があり、システム操作に長い時間を取られるのは困ります。その点、本システムは1回のチュートリアルと数回のリハーサルだけですぐに使い方を覚えられるほど、操作が簡単です。さらに処理時間についてもほんの数秒で、普段自分が判断するよりずっと早く業務でも十分使えると感じました。」
本システムのUXデザインを担当した武内は、配慮したポイントを次のように語ります。「当初はPCを用いた利用を想定していたのですが、熱や煤の出る製造現場の環境では操作性、耐久性共に問題があり、以前から中島合金様が活用されている防護ケース付きのタブレットでの操作に切り替えました。また、製造業界ではMicrosoft Office製品群を利用しているユーザーが多いことから、そのような方が普段システムを使う感覚で利用できる操作性を目指しました。」
<適応的未然防止について>
適応的未然防止とは、名古屋工業大学名誉教授 仁科健氏によって提唱されている品質のばらつきを抑える4つのアプローチのうちの1つで、「原因の状況を見て、結果にアクションする(調整する)」方法です。
結果のばらつきはそこに寄与する原因のばらつきによって引き起こされるため、本来的には原因のばらつき自体を抑える取り組みが必要です。しかし、製造の現場では必ずしもすべての原因を制御できるわけではなく、技術的コスト的制約の中でばらつきを受容するしかないものも存在します。
このような抑えることのできないばらつきに対して、適応的未然防止のアプローチは有効となります。
例えば、金属熱処理の焼き入れ工程において、材料のカーボン量がJISの許容範囲内でばらついている場合、それが原因となって焼き入れ硬度にもばらつきが生じます。
このとき、材料のカーボン量を事前に測定することによって焼き入れ温度を調整することで硬度のばらつきを抑える、というようなアプローチを指します。
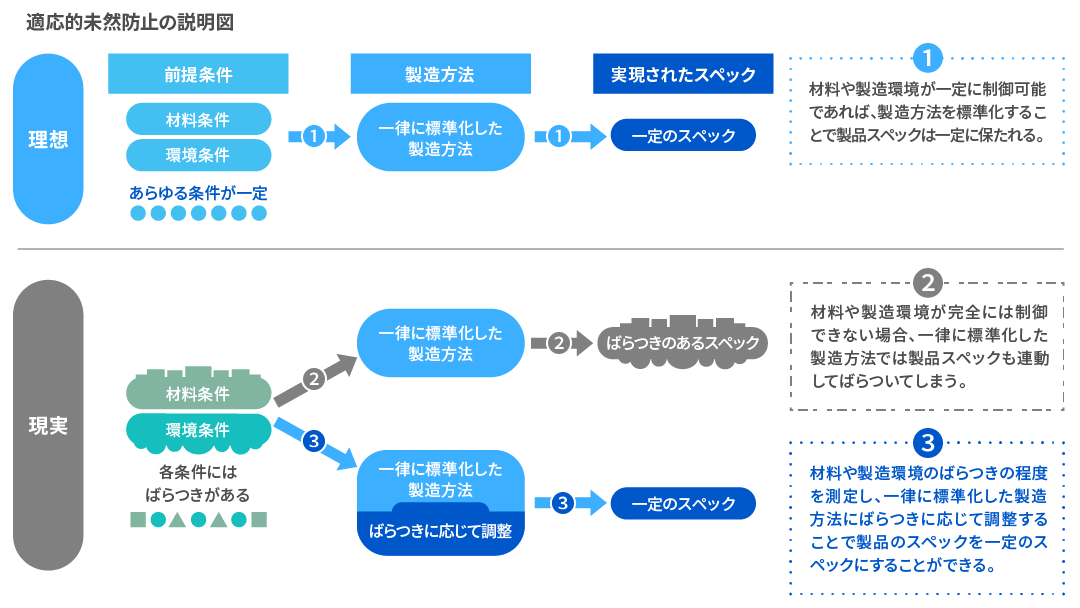
成果・総評
本実証実験で得られた成果は、次の通りです。
<中島合金様>
・安定した製造による生産性の向上(製造リードタイム短縮、品質の維持向上)
・コア技能の属人化防止と若手が早期に技能継承を実現
・働き方改革の推進(熟練者の休暇取得がしやすくなる、心理的プレッシャーからの解放)
・事業継続性の確保
「今回検証したAIの仕組みがあれば、熟練者が急に休む状況になっても経験の浅い技術者でも対応でき、製造スケジュールの変更や、納期が遅延してお客様にご迷惑をかけるといったことも防げます。製造業の企業では、この人がいなければこの作業ができないであるとか、熟練者が複数の重要な業務を兼任している状況が多くあります。こうしたシステムが実用化されることで役割分担ができ、現場の作業者の負担が軽減されることを期待しています。」
(中島合金 製造部 生産管理課 小林達生氏)
「IoTやDXが叫ばれる製造業において、どのようなデータを取得すれば何が起因なのかの発見につながり、結果としてどういった施策に活かせるのか、イメージが捉えにくい点が課題であると感じていました。今回の実証実験ではしっかりデータを取得していけば将来、人による判断や、人が予測しきれない、管理しきれない点においてもAIで補うことができて、熟練者だけしか対応できない業務を減らすことができる可能性を感じました。少子高齢化の進む日本では、外国人の雇用もさらに進みます。その際には、数値でガイドラインを示すことが求められるでしょう。私自身は直感や勘による判断というものも、データ化できると考えています。」
(中島合金 代表取締役社長 中島一郎氏)
<三菱総研DCS側>
・ソフトウェアの現場における活用イメージの把握
・業務内容を把握するために必要なタスクおよび期間の把握
・機密情報提供を受ける際の契約締結など諸手続きの必要性を把握
・現場作業者が利用しやすいUIの開発、および理想的なUXの実現
「今回の実証実験により、予測機能に関して、AI予測値の妥当性とシステムの操作性が実用に耐えうるレベルであると確認できました。そこで今後は、予測機能の前段である学習機能を強化していきます。
現状では、学習機能に関して『AI技術のインスタント化』という我々の目指すところにはまだ至っていません。現場で新たなテーマが見つかった時にデータサイエンティストの支援を必要とせず、すぐにご自身で試せる操作性を目指して改良を重ねます。
加えて、高精度な学習には投入データの質が重要となるため、データ項目は足りているのか、それとも余分なものが混入しているのか、データパターンは十分なのかを助言する機能の開発も検討しています。これら開発には現場の実状を把握し、そこで働く方々の声に丁寧に耳を傾ける必要があると考えておりますので、製造現場の声を教えていただくパートナーとして、中島合金様には今後とも是非ご協力いただきたいと考えています。
また、AI活用には熟練者の方を代替するようなイメージがどうしても強いのですが、我々はかねてより『AIは、役割分担により熟練者の負担を軽減し、熟練者をさらに輝かせるためのものである』と考えています。今回の実証実験を通じて、改めてその思いを強くしました。
AIはあくまでも、熟練者の方がこれまで確立してこられた作業標準とそれに基づく精緻なデータを前提にして初めて効果を発揮します。その結果としてAIが役割分担できれば、熟練者の方はまた新たな作業標準の確立という高難度の業務に時間を割くことが可能となります。それがまた新たなAIの生成につながっていく。
AIと熟練者が協働して、工程全体の生産性と品質を向上していく新たな業務スタイルを広めていきたいと考えています。」
(三菱総研DCS シニアデータ分析エンジニア 永田貴弘)
当社は本実証実験の結果を踏まえ、現在は大企業のみに限定されているデータ利活用の恩恵を中堅・中小企業にも拡大することで、日本の重要産業である製造業のDX(デジタルトランスフォーメーション)を推進するためのサービス開発に引き続き、取り組んでまいります。
- Microsoftの商標およびロゴは、米国およびその他の国におけるMicrosoft Corporation および/またはその関連会社の登録商標または商標です。
-
お問い合わせ
-
本サービスの詳細につきましては、以下お問い合わせフォームよりご相談ください
関連するソリューション・サービス
関連する技術レポート・導入事例
メディア掲載・登壇実績
- 上記から各外部サイトへ遷移します。