製造業・熟練技能者の暗黙知をAIに代替させる実証実験を開始
2021.12.13
- AI
- 製造業
- 業務効率化
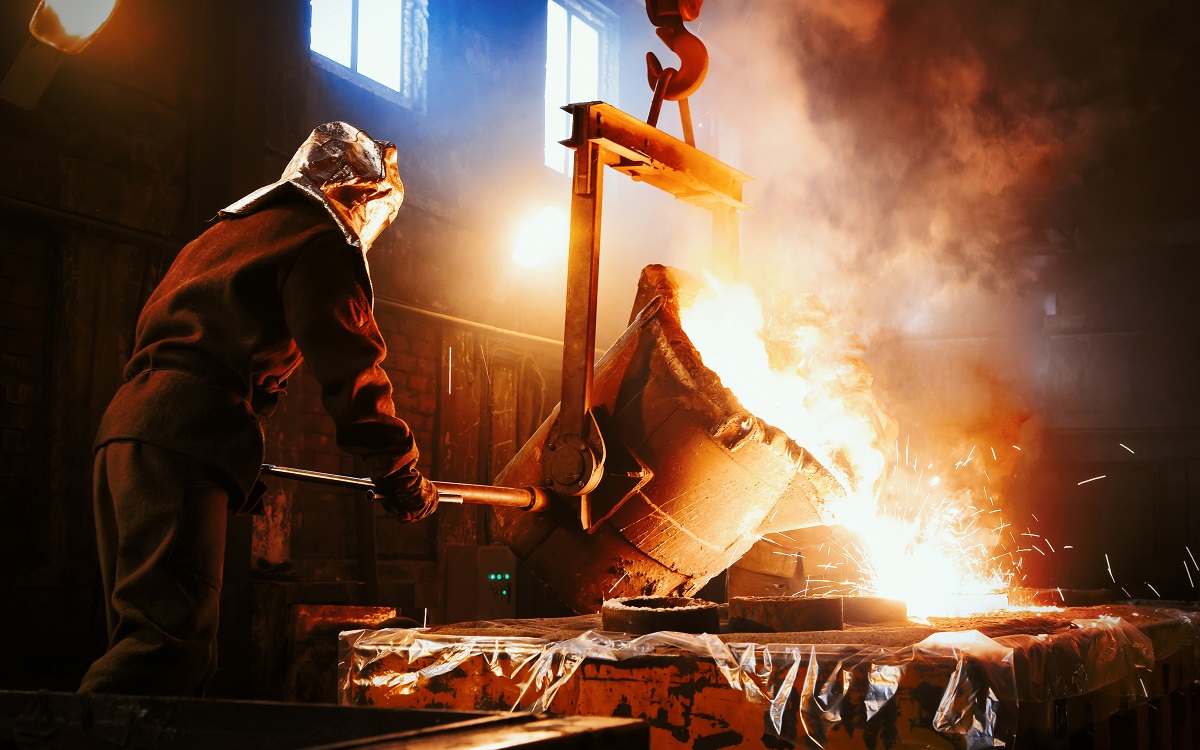
当社は中島合金株式会社様(以下、中島合金様)と共同で、純銅鋳造製造工程における熟練技能者の暗黙知をAIに代替させる実証実験を開始しました。
本稿では本実証実験の必要性と手順、期待効果について、詳細を解説します。
<実証実験概要>
- 期間 2021年12月
- 対象業務 純銅鋳造製造における添加剤の投入量判断
- 検証観点 ・AI予測値の妥当性
・現在の業務への適合性
・システムの使いやすさ
本実証実験実施の狙い、背景
難しいAI技術を現場技術者でも利用できるよう、インスタント化
すべての製造企業に「データ分析のチカラ」を!
製造現場における主たる課題として、人材不足、生産性向上、熟練職人による技術の属人化が挙げられます。また、社会のデジタル化と働き方改革への対応および、若手への技能継承による事業継続性の確保も求められており、その対応策としてデータ・AI利活用ニーズが高まり、実用に向けた動きが加速しています。
しかしながら大企業に比べ資金力や人員数が劣る中小企業では、データ利活用のための投資予算や対応するデジタル人材の確保が難しく、導入検討が進んでいない現実があります。総務省「2020年ものづくり白書」によれば、デジタル技術を「すでに活用している」と回答した企業は約半数の49.3%、「未活用」と回答した企業も46.4%と拮抗。そして活用企業の割合では大企業が60.8%である一方、中小企業は48.5%にとどまっています。
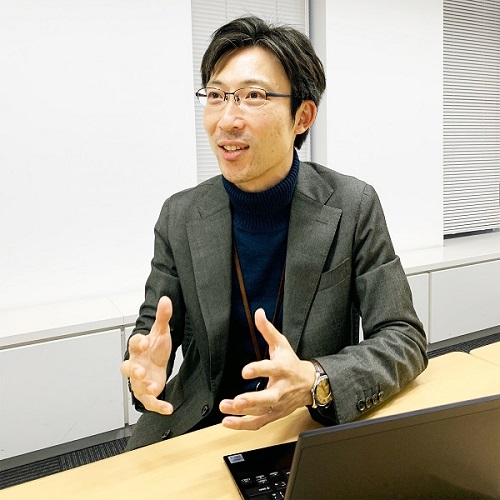
シニアデータ分析エンジニア 永田貴弘
当社のシニアデータ分析エンジニアである永田は、
「従来の多くのデータ分析ソフトウェアは統計学や機械学習の深い知識を前提としており、製造の現場技術者が使うには操作の習得に時間がかかるなど、導入のハードルが非常に高い。当社はこの課題に対応すべく、『難しい操作を難しく感じさせない、AI技術のインスタント化』を製品コンセプトに開発を進めています。
AIのオートチューニングアルゴリズムとUXデザインを駆使し、『データサイエンスの知識がない現場技術者でも高いハードルを感じずに利用可能なデータ分析ツール ※ 』としての開発精度をより高めるべく、中島合金様の協力を仰ぎ、実証実験を行うこととしました。」 と語る。
※特許出願中
解決すべき課題
熟練者のみが把握する「暗黙知」をAIに代替させ、
企業競争力の源泉である独自技能の次世代への継承を実現させる
中島合金様は、2020年に創業100年を迎えた銅合金鋳物・アルミニウム合金鋳物に加え、鋳造に高度な技術が必要とされる純銅鋳物を得意とする鋳造メーカーです。古い技術を伝承しつつ機械化を進めることで研究や生産を100年積み重ねた実績は、他社では真似のできない独自製法の確立となり、お客様のニーズに合わせた品質の高い製品作りに繋がっています。
純銅鋳物にはCAC100番台のJIS規格が定められており、品質を一定水準に揃える必要があります。一方、その製造工程には原材料自体の状態や、気温・湿度など制御できない条件が存在しており、製造条件のばらつきが避けられないことが純銅鋳造の難しさの一因となっています。
中島合金様は、製造工程の途中段階でばらつき具合を測定し、その値に応じて調整用の添加剤を適切量投入することで製品の最終品質を均一化するノウハウがあります。しかし、この技能は熟練者のみが把握する「暗黙知」であり、若手が継承するには長い時間がかかるとの課題意識がありました。
そこで、中島合金様とDCSはこの課題解決に着手し、AI技術を活用して「製造時のばらつき状態」と「添加剤の投入量」の関係を学習することで、熟練者の判断を再現できることが確認できました。
本実証実験では、このAIの判定精度を向上させるだけでなく、予測時間が実用に足るか、また製造の現場技術者が利用するシステムとして操作性に問題はないかなど、システム全体としての業務適用可否を検証いたします。
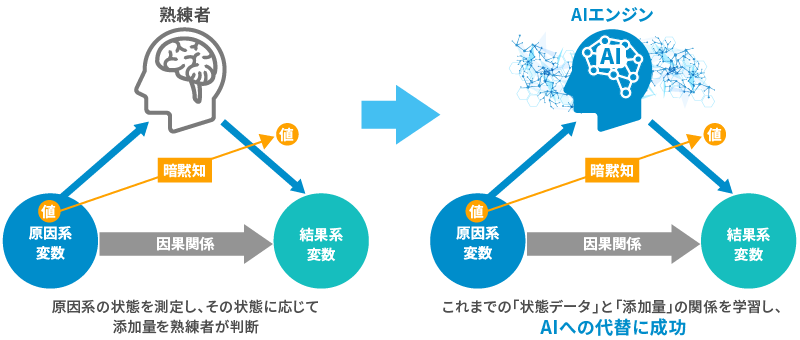
<品質のばらつき低減へのアプローチ:「適応的未然防止 ※1 」>
今回、本実証実験は愛知工業大学 経営学部 経営学科 仁科健教授 に品質管理の分野でどのように考えられるのか相談にのっていただきました。
仁科教授は製造工程における品質のばらつきの「原因」「結果」「因果関係」へのアクションの取り方を観点として、ばらつき低減のアプローチを体系化されています。本事例はその中の「適応的未然防止 ※1 」に該当するとお話しいただきました。
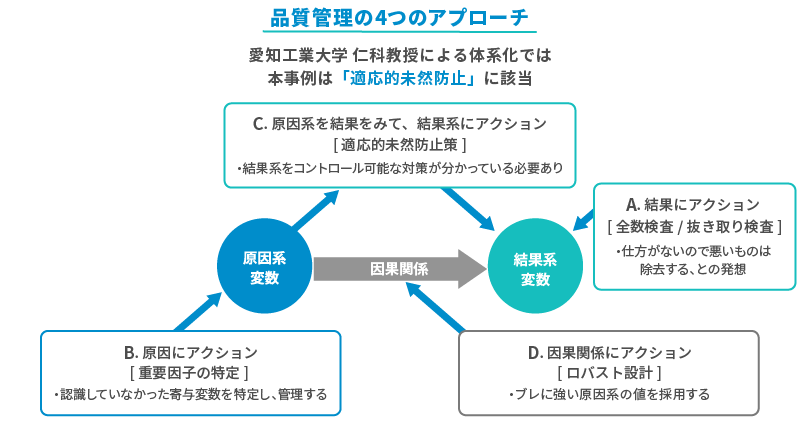
>参考:『品質のつくり込みは「ばらつき」への挑戦』(仁科(2009):統計的工程管理,朝倉書店)
- 適応的未然防止とは:仁科教授によって体系化された品質管理の4つのアプローチのひとつで「原因の状況をみて、結果にアクションする(調整する)」方法です。
実証実験詳細(実施手順/期間)
約1か月で熟練者の暗黙知をAIに代替させる実証および業務プロセスにおける適合性検証を実施
本実証実験は約1か月を予定しており、以下の手順と期間で進められます。
(N:中島合金様/D:三菱総研DCS)
ステップ1:課題のヒアリング、業務知識の習得 / 1週間
両社:製造現場における課題の詳細をヒアリング、両社で解決策を協議
D :並行して今回の対象である鋳造業務の業務知識を習得
(現場視察および技術者からの指導を受ける、関連資料・論文などを読むなどにより、現場の技術者と互角に会話できるレベルを目指す)
ステップ2:データの提供、AIによる学習 / 2週間
N :過去の製造工程における原因系(原料/気温など)、結果系(製品の品質)および、アクション(調整用の添加剤投入量)の詳細データを提供
D :提供データに必要な加工を施し、AIに学習させる
ステップ3:AIが算出したデータを実業務で照合 / 3日間
両社:実際の業務においてAIの予測数値を熟練者の算定数値と照合(計10度)
ステップ4:AIが算出した数値での製造、品質検査 / 3日間
両社:AI予測数値により実際に製造を行い、出荷可能な品質たりえるかを検査
UXの改良 / 上記期間と並行して実施
また、三菱総研DCSは上記の実証実験工程と並行して、現在プロトタイプである本解析システム画面上の操作しやすさ、わかりづらい点などのフィードバックを受け、「製造現場の担当者でも簡便に扱える操作性」を目指して、さらなるUXの改良も行います。
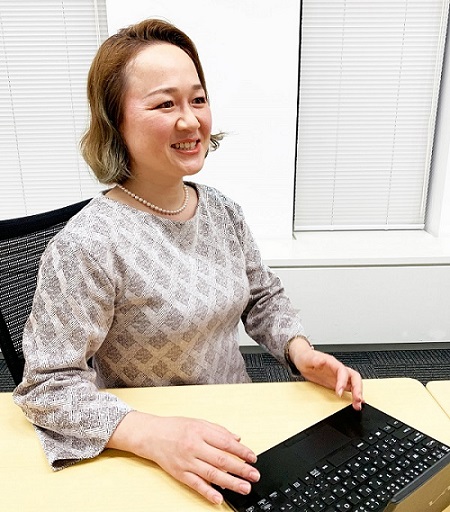
HCD-Net認定 人間中心設計専門家 武内亜美
当社のUXデザイナーである武内は、
「使いやすいソフトウェアの開発には、ユーザーの利用状態を正しく把握する必要があります。今回の実証実験では中島合金様のご協力で、利用者の方々が働く現場や使用デバイスなどの環境面、また開発中の画面を実際に使用いただくことで操作性も詳細に把握できると期待しています。
得られた情報を開発にフィードバックすることで、本サービスのコンセプトである『データサイエンティストなどの専門家でなくても、現場技術者が利用しやすいソフトウェア』を実現したいと考えています。」 と語る。
本実証実験で期待される成果と価値
生産性向上、若手の技能継承と事業継続性に貢献すると共に、
日本を支える中堅・中小製造企業のDXを推進
本実証実験で期待される成果は、次の通りです。
中島合金様
- 安定した製造による生産性の向上(製造リードタイム短縮、品質の維持向上)
- コア技能の属人化防止と若手が早期に技能継承を実現
- 働き方改革の推進(熟練者の休暇取得がしやすくなる、心理的プレッシャーからの解放)
- 事業継続性の確保
三菱総研DCS側
- ソフトウェアの現場における活用イメージの把握
- 業務内容を把握するために必要なタスクおよび期間の把握
- 機密情報提供を受ける際の契約締結など諸手続きの必要性を把握
- 現場作業者が利用しやすいUIの開発、および理想的なUXの実現
三菱総研DCSは本実証実験の実施により、これまで難度の高かったAIによる分析を現場作業者にも容易に扱える操作性を実現し、実業務への適合性、導入コストも含めた「インスタント化」を実現。本サービスの実用化により、現在は大企業のみに限定されているデータ利活用の恩恵を中堅・中小企業にも拡大することで、日本の重要産業である製造業のDX(デジタルトランスフォーメーション)を推進いたします。
今後の展開
2021年12月に本実証実験を実施。その後も本サービスの実用化に向けた検証を、継続してまいります。
また、三菱総研DCSではさらに本サービスの適用範囲を拡大する目的で、並行して他の製造業企業においても複数の実証実験を予定しております。
-
お問い合わせ
-
本サービスの詳細につきましては、以下お問い合わせフォームよりご相談ください
関連するソリューション・サービス
関連する技術レポート・導入事例
メディア掲載・登壇実績
- 上記から各外部サイトへ遷移します。